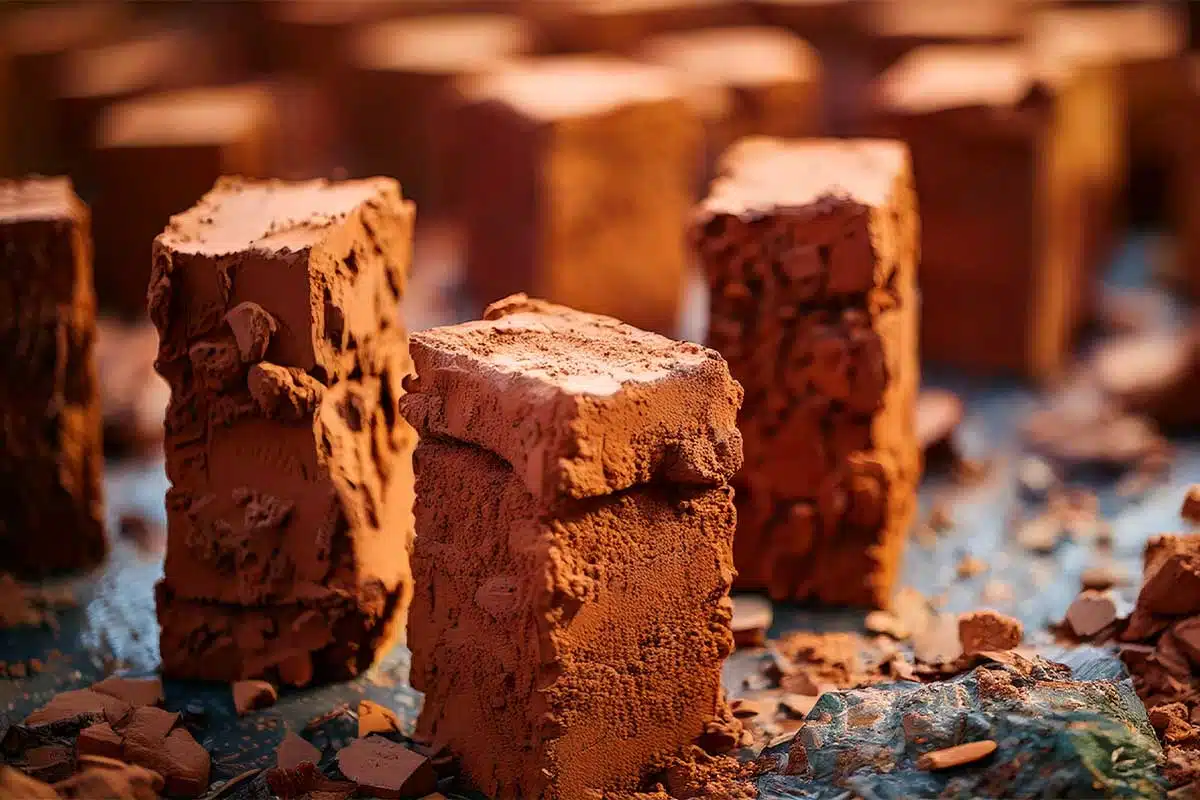
Je ne sais pas vous, mais, personnellement, quand j’entends parler de liant bas-carbone qui pourrait remplacer le ciment, je tends l’oreille. Est-il besoin de vous rappeler que l’industrie du ciment est responsable de plus de 7 % des émissions mondiales – soit quelque 2,5 milliards de tonnes selon Ecocem ? À Saint-Maximin, dans l’Oise, l’entreprise NeoCem vient d’inaugurer son premier site industriel de flash-calcination d’argile. Le concept ? Reprendre une technique que les Romains utilisaient déjà, mais en version 2025. Résultat : un ciment plus écologique, fabriqué à partir d’argile de récupération issue… des déblais du Grand Paris Express. Comme quoi, les gravats d’aujourd’hui peuvent devenir les fondations de demain. Présentation de ce concept très innovant et, je l’espère, prometteur.
Une idée simple, un procédé intelligent
Derrière NeoCem, on trouve les fondateurs de Neo-Eco, un groupe spécialisé dans l’économie circulaire. Leur credo : donner une seconde vie à des matériaux destinés à l’oubli. Ainsi, l’argile récupérée des chantiers du Grand Paris, ils ont décidé de ne pas la laisser filer. Grâce à un procédé de flash-calcination, l’argile est transformée en un liant prêt à remplacer une partie du ciment traditionnel. On parle ici de 100 000 tonnes par an, avec un objectif de 200 000 tonnes à court terme. Ainsi, contrairement aux extractions classiques, aucune nouvelle carrière n’est creusée : tout vient des déblais existants. Résultat ? Moins d’impact environnemental, et une valorisation concrète d’un matériau souvent considéré comme un simple rebut.
Un ciment plus vert, sans sacrifier l’efficacité
La force de NeoCem, c’est de conjuguer écologie et performance. Le liant obtenu permet de produire des ciments LC3, avec une composition équilibrée : un tiers de clinkers (le plus décarboné possible), un tiers de filler calcaire, un tiers d’argile calcinée. Ce type de mélange réduit l’impact environnemental du béton, tout en restant conforme aux nouvelles normes en vigueur. Et, comme la demande nationale en ciment atteint 18 millions de tonnes par an, les marges de progression sont énormes. Sans oublier que l’ensemble du procédé est breveté, optimisé pour consommer moins d’énergie. Bref, on reste dans l’efficacité… sans exploser le bilan carbone. Ainsi, ce n’est pas un effet d’annonce : la technologie développée a nécessité quatre années de R&D rigoureuse, avec des partenaires comme l’Ademe et Mines-Télécom Nord-Europe.
Un modèle local et duplicable
Le site de Saint-Maximin est seulement le début. NeoCem prévoit de dupliquer ce modèle industriel dans d’autres régions françaises, en s’implantant près des ressources disponibles. En effet, de l’argile « usagée », il y en a un peu partout. L’objectif ? Créer une filière nationale, relocaliser la production, et montrer qu’on peut faire du béton autrement. Avec déjà une joint-venture en vue, et des partenariats solides comme les Carrières du Boulonnais, la dynamique est bien lancée. Et, tout ça, sans renier le bon sens des Romains : réutiliser ce qu’on a, au lieu de toujours produire du neuf.
Produire mieux, localement, sans sacrifier l’efficacité ni l’économie, c’est le pari de NeoCem. Pour une fois, il semble bien parti pour être tenu. Plus d’informations : ecocemglobal.com. Et vous, seriez-vous prêts à construire ou rénover avec un liant bas-carbone, fabriqué à partir de déblais recyclés et d’argile flash-calcinée, comme chez NeoCem ? Ce sujet vous intéresse ? N’hésitez pas à nous donner votre avis, ou à partager avec nous, votre expérience. Merci de nous signaler toute erreur dans le texte, cliquez ici pour publier un commentaire .