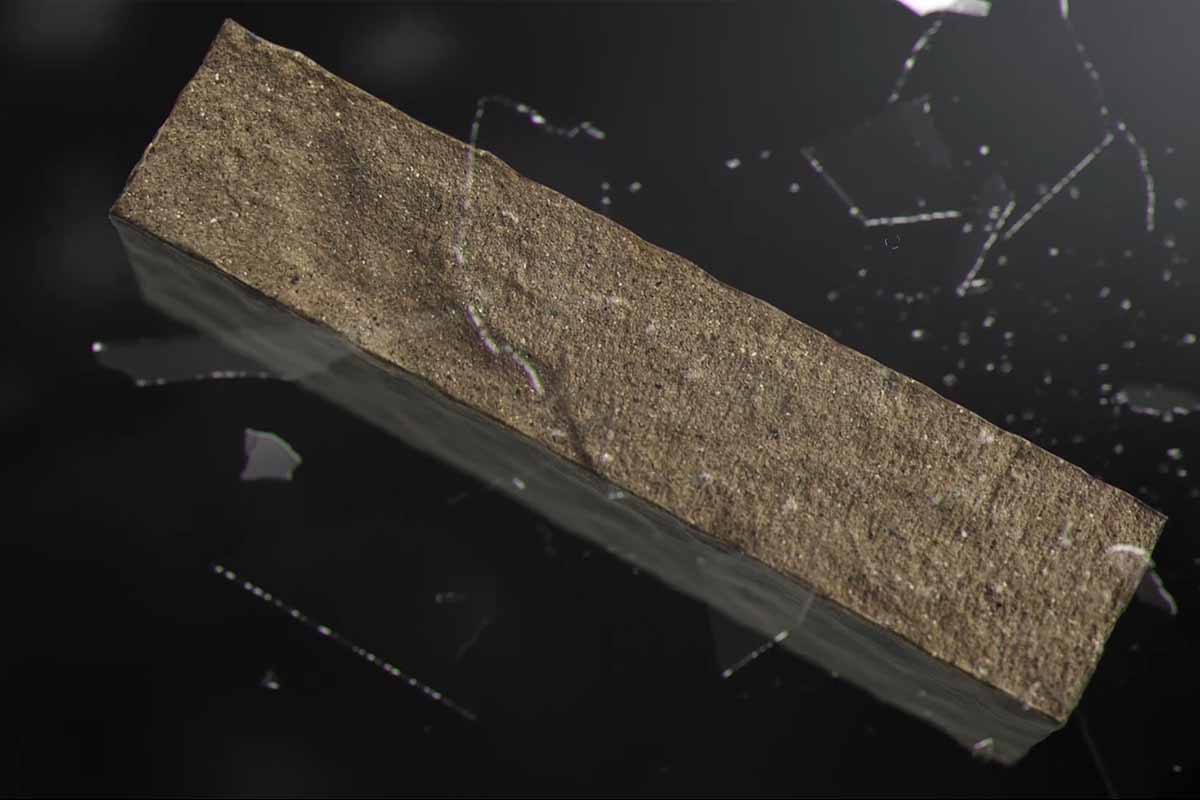
La capture du dioxyde de carbone fait partie des solutions de décarbonation recommandées afin d’atteindre l’objectif « net zéro émission » d’ici à 2050. Cette méthode convient principalement à l’industrie lourde qui utilise encore de grandes quantités d’énergies et de combustibles fossiles. Lorsque le CO₂ est capté, les usines ont le choix de le stocker ou de le valoriser. C’est à ce stade que d’autres entreprises peuvent intervenir pour exploiter ce gaz, en vue de fabriquer des produits bénéfiques à l’Homme (les e-carburants par exemple). L’entreprise Vandersanden a notamment eu la brillante idée d’utiliser le dioxyde de carbone dans le processus de séchage de ses briques de parement, au lieu de recourir à la méthode de cuisson à haute température (900 à 1 200 °C). Cette innovation présente plusieurs avantages, dont le stockage du CO₂ capté et la baisse significative des émissions de gaz à effet de serre dans le secteur de la construction. Nous vous fournissons plus de détails sur ce nouveau type de brique dans cet article.
Comment cette nouvelle brique est-elle fabriquée ?
Basée à Limbourg, en Belgique, la briqueterie familiale Vandersanden a collaboré avec la société Orbix, sise à Genk, pour réussir ce défi de produire des briques de parement négatives en CO2. Forte de son expérience de près de cent ans, cette briqueterie a adopté un procédé industriel développé par Orbix. Cette technique révolutionnaire se base sur le processus naturel de carbonatation, durant lequel l’apport du dioxyde de carbone solidifie les matériaux. Ces derniers se transforment ensuite en carbonate de calcium (CaCO3). En pratique, les briques sont durcies dans une salle remplie de dioxyde de carbone récupéré par les usines dans l’industrie lourde, en particulier les usines métallurgiques. Selon les responsables, une tonne de briques de parement est capable d’incorporer environ 60 kg de dioxyde de carbone.
Comment a été créée la salle de séchage pilote ?
L’entreprise Vandersanden a engagé le laboratoire CEE, situé à Hamme-Mille, pour modéliser et tester le procédé de durcissement ou de séchage des briques Pirrouet. En effet, le matériau doit capter le dioxyde de carbone dans des conditions parfaitement contrôlées (température, humidité, débit d’air, temps de séchage). De plus, il est important d’arriver à créer un environnement approprié dans la chambre de séchage afin d’obtenir des briques de qualité supérieure à chaque processus de production.
CEE a donc pris en charge l’ingénierie de base de cette salle à l’échelle industrielle, dans le cadre du projet expérimental. Celle-ci a été préfabriquée dans les ateliers CEE, situés à Herentals. Ensuite, elle a été déployée sur un site de Vandersanden à Lanklaar en 2020. Ce qui a permis à cette entreprise de développer sa nouvelle brique qui absorbe le CO₂ au lieu d’en émettre.
Ce nouveau type de brique est-il écologique ?
Grâce au nouveau processus basé sur la carbonatation, la fabrication des briques de parement consomme moins d’énergie et ne débouche pas sur des rejets de gaz à effet de serre. Ces matériaux de construction constituent une solution de stockage de dioxyde de carbone durable et écologique. Outre cela, la société Vandersanden estime que ses nouvelles briques de parement soutiennent l’économie circulaire. Celles-ci seraient composées de matières premières primaires (20 %) et de déchets minéraux provenant de l’industrie métallurgique (80 %). À partir de 2024, cette briqueterie européenne prévoit de produire 20 millions de briques par an. Une première usine est actuellement en cours de construction en Belgique. Plus d’informations : Vandersanden.com
Que pensez-vous de cette technologie ? N’hésitez pas à partager votre avis, vos remarques ou nous signaler une erreur dans le texte, cliquez ici pour publier un commentaire .