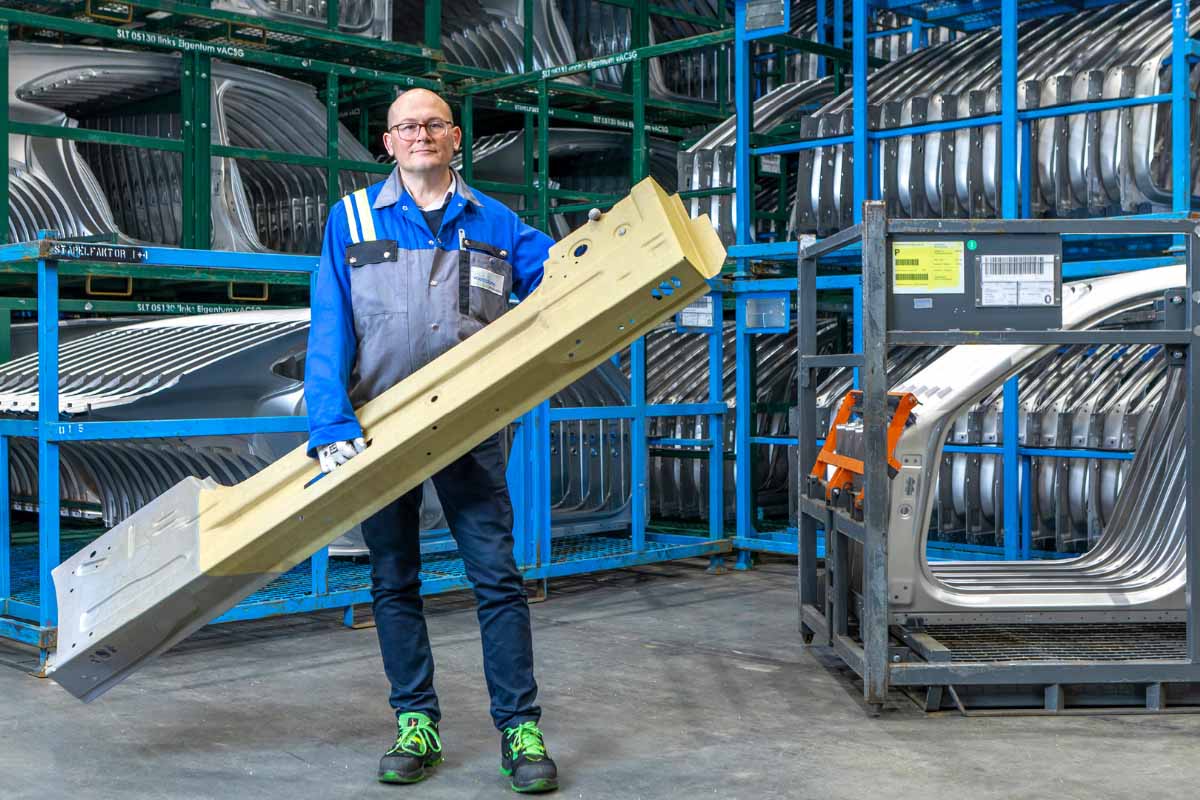
Grâce à la découverte d’un nouveau procédé de zingage largement prometteur, un groupe de recherche affilié à l’entreprise autrichienne Voestalpine est devenu finaliste du prestigieux concours « Prix de l’inventeur européen 2023 ». L’équipe, constituée par Josef Faderl, Siegfried Kolnberger, Thomas Kurz et Andreas Sommer, a développé un nouveau type d’acier qui est à la fois plus léger et plus résistant que l’acier conventionnel. De plus, il résiste mieux à la corrosion et peut être facilement fabriqué en grande quantité. Ce matériau s’adresse principalement à l’industrie automobile. Depuis sa mise en production en 2008, cet acier de nouvelle génération est utilisé pour fabriquer en moyenne environ 30 millions de pièces automobiles par an.
Pressage à chaud
La technologie, élaborée pour la première fois en 2002 et baptisée PHS Ultraform, vise à améliorer le traitement de l’acier par galvanisation. Mettant en œuvre une technique connue sous le nom de pressage à chaud, elle consiste à exposer le métal à des températures extrêmement élevées avant de le refroidir rapidement dans une presse. Ce procédé permet de concevoir des pièces en acier ultra résistantes avec des géométries complexes. Cependant, il ne protège pas le métal contre la corrosion. Les chercheurs ont alors inventé un nouveau type de revêtement obtenu à partir d’une solution à base de zinc. Le traitement anticorrosif traditionnel utilise généralement la technique du trempage aluminium-silicium. Mais comme ce mélange protège moins l’acier par rapport au zinc, ce dernier est davantage privilégié pour la galvanisation.
Empêcher l’évaporation du zinc
Il y a toutefois un problème avec le zinc. Il fond à 420 °C et s’évapore au-delà de 900 °C. Or, le pressage à chaud se déroule à très haute température. Pour surmonter ces contraintes, les scientifiques ont cherché une solution capable d’empêcher l’évaporation du zinc lors de la phase d’application du revêtement. Ils ont découvert que l’ajout d’une petite quantité d’aluminium entraînait la formation d’une très fine couche d’oxyde d’aluminium sur ledit revêtement, rendant possible le pressage à chaud à très haute température. Le résultat est un acier plus léger et plus résistant, doté de propriétés anticorrosion améliorées.
Plus respectueux de l’environnement
Par ailleurs, l’autre avantage de cet acier innovant est qu’il est entièrement recyclable. Cela donne aux constructeurs automobiles la possibilité d’utiliser moins de matériaux issus directement des ressources naturelles. Il va sans dire que le recyclage aide également à réduire les émissions de gaz à effet de serre lors de la fabrication des pièces. Grâce à leur légèreté, ces dernières permettent de concevoir des véhicules moins lourds, ce qui a un impact direct sur la consommation de carburant. Enfin, l’amélioration de la résistance aux chocs offre une meilleure protection en cas d’accident. Plus d’info : epo.org. Que pensez-vous de cette invention ? N’hésitez pas à partager votre avis, vos remarques ou nous signaler une erreur dans le texte, cliquez ici pour publier un commentaire .
Bravo aux 21e siècle on doit rattraper le retard en évolution.
une évolution dans le domaine alimentaire serait bien venu.
Tu penses certainement à ingurgiter des insectes!
Belle invention ,très intéressante surtout pour la corrosion et le poid qui devrait nous faire arriver a des consomation de 0,5 litre a nos vitesse de 80 kmh en voiture ou bien a 0,3 litre sur nos gros cube moto toujours a 80 aller 85 kmh ,c’est génial vive la progression
Même en cette période de Noël, il faut être prudent dans ce que l’on peut lire.
Le procédé d’emboutissage à chaud existe effectivement depuis longtemps. Il permet de former des pièces avec un acier plus résistant, rendu plus malléable par la chaleur. Alors oui la pièce va être plus résistante à masse égale ou plus légère à même résistance, car plus fine. Mais cela ne rend pas l’acier plus léger …
Et si ce procédé n’est pas plus utilisé aujourd’hui c’est en raison de son coût : l’acier est plus noble donc plus cher et il faut apporter de l’énergie pour produire la chaleur.
La vraie innovation concerne la protection anti corrosion mais à la marge en terme de masse les épaisseurs de zinc faisant en très grande majorité entre 7 et 10 microns dans l’automobile.
J’apprécie le procédé et me demande quelles pourraient en être les appli ations au domaine du bâtiment en Afrique ou l’utilisation du bois dans les structures porteuses en infrastructure ou en toiture est fortement mis à mal par la difficulté de trouver du « bon bois ».
Merci neozone pour tous vos partages.
Si la réduction de poids est sans aucun doute en effet bénéfique en terme de consommation et donc d’émissions de CO2, difficile de savoir sans plus d’informations si c’est une « bonne » invention socio-environnementale :
1) Socio car si la résistance accrue protège les passagers de la voiture équipée de cet acier, quid de ceux qui seraient en face #compatibilité
2) Environnementale car ce matériau semble utiliser des matières premières très « classiques », un procédé de production et mise en forme à très hautes températures (donc très consommateur / émetteur). Enfin, si le 100% recyclable sonne toujours bien, il faudrait savoir à quel coût énergétique.
Le diable peut se cacher malheureusement dans les détails.
Très cordialement et coopérativement, Nicolas
C’est pas une vraie découverte ! Ils font galvaniser la tolle, pour plus jamais pouvoir réparer les pièces, vivent la pollution de la terre
Faut faire des caisses en inox.
Et surtout faire des voitures faciles à démonter.
ET LIMITER LA TAILLE DES BATTERIES À 80 kWh pour les petits modèles est 100 kWh pour les grosses familiales
On pourrait passer directement à la marche arrière, ce qui permettrait d’arriver avant d’être parti!
Intéressant, 6 fois plus solide, c’est vague !
Les pièces seront elles plus fine pour être plus légère ou seront elles plus légère avec les même cotes que l’acier précédent ?
De plus ni cette article ni celui indiqué en conclusion ne donne d’idée sur le gain de poids théorique pour un véhicule. Beaucoup de promesses et de spéculations qui laissent sur sa faim.
Ne pourrait on pas réaliser des modèles en acier inox recyclable à l’infini. Pour les pièces extrêmement sollicitées, les réaliser en titane lui aussi inoxydable et recyclable serait la solution ?